On the 8th of February 2023, Mimas was moved from Bainfield Student Accommodation to Merchiston Campus, room D66.
Thanks to Brian Davison, Alexandros Gkanatsios and Stuart Thomas, we got access to a brand-new laboratory to work on the rover! The lab has a workstation for soldering, whiteboard tables for sketching (and, most importantly, a lot of convenient electric plugs!).
It took several hours to pack Mimas, ensuring she is safe during the journey from Bainfield to Merchiston, and when the rover arrived at its destination, the help from the ENU Formula Student team was invaluable. Mimas will stay in D66 for 8 weeks and during this relatively short period of time, it will undergo several changes, wiring, and drive testing. As the Honours Project report submission day gets closer and closer, the construction of the rover becomes more challenging.
- [Hours of work: 6]
- [People involved: Giorgio, Akshit, w/ENU Formula Student team]
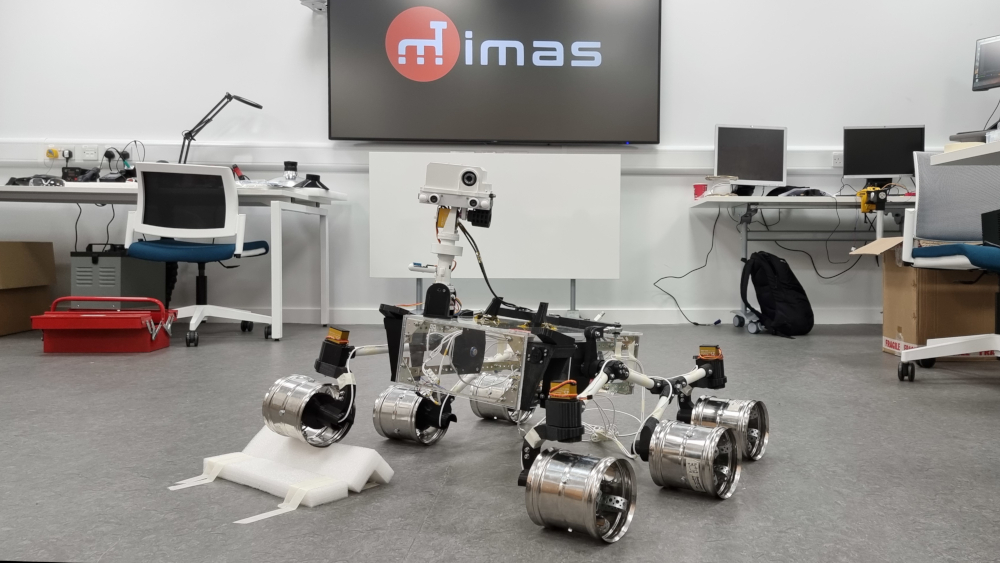